In the vast world of industrial and chemical processes, evaporators play a crucial role in transforming liquids into vapors through controlled heating. But what is the most widely used evaporator, and why does it stand out among the many types available? Let’s dive into this fascinating topic and unravel the secrets behind the most popular evaporator types.
Types of Evaporators
Before identifying the most widely used evaporator, it’s essential to understand the different types and their classifications. Evaporators can be categorized based on various factors, including solution circulation, evaporation mode, operating pressure, and the number of effects.
- Circulating Type Evaporators:
- Natural Circulation: Examples include the central circulation tube evaporator and the suspension basket evaporator. These rely on natural convection currents created by differences in fluid density within the heating chamber.
- Forced Circulation: These evaporators use pumps to circulate the solution through the heating surface, ensuring efficient heat transfer.
- Single-Pass Type Evaporators:
- Solutions pass through the heating surface only once before being discharged as concentrated liquid. Types include rising film, falling film, stirred thin-film, and centrifugal thin-film evaporators.
- Direct Contact Type Evaporators:
- Heating medium and solution come into direct contact, such as in immersion combustion evaporators.
The Most Widely Used Evaporator: Central Circulation Tube Evaporator
Among the myriad of evaporator types, the central circulation tube evaporator (also known as the standard evaporator) stands out as the most widely used. Here’s why:
- Structure and Operation:
- The heating chamber comprises vertical tube bundles with a large central circulation tube surrounded by smaller boiling tubes.
- The solution forms a natural circulation due to density differences between the heated solution in the boiling tubes and the less heated solution in the central tube.
- The upward suction of vapor enhances this circulation, leading to efficient heat transfer.
- Advantages:
- Compact Design: Its streamlined structure makes it easy to install and maintain.
- Manufacturing Simplicity: The design is straightforward, reducing production costs.
- Reliability: Proven to be robust and reliable in various industrial applications.
- Applications:
- Used extensively in chemical, food processing, and pharmaceutical industries where continuous and reliable evaporation is crucial.
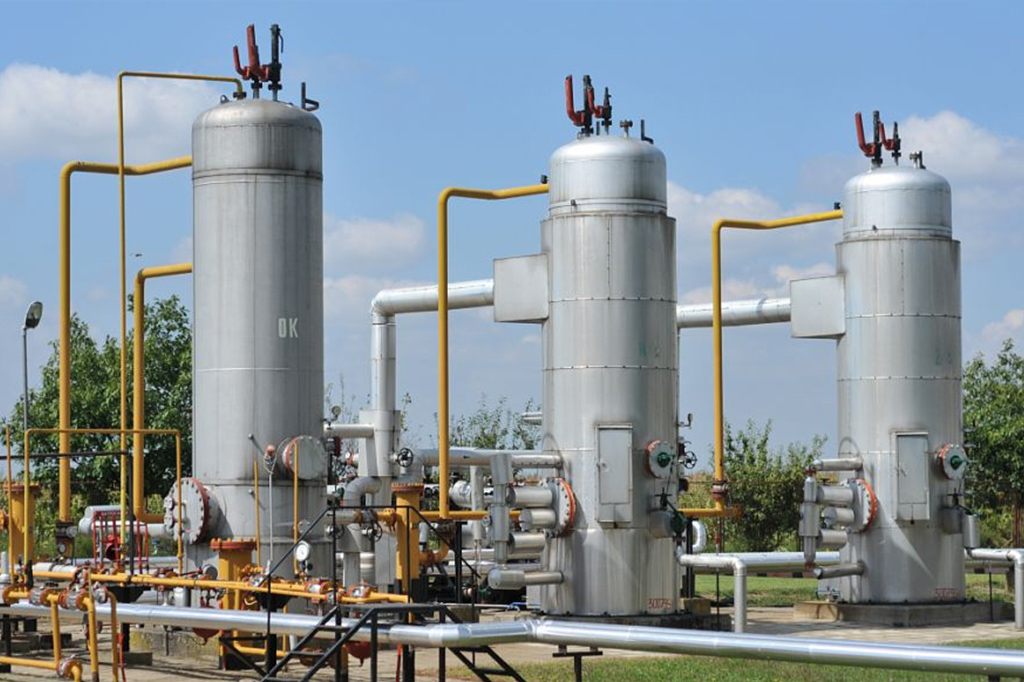
Why It’s Popular
- Versatility: Its design allows it to handle a wide range of solutions, from low to high viscosity.
- Efficiency: Although it shares the common limitation of cyclic evaporators—decreasing effective temperature difference due to concentration—its simplicity and reliability often outweigh this drawback.
- Scalability: Can be scaled up or down to suit different production capacities.
Other Notable Evaporators
While the central circulation tube evaporator reigns supreme in popularity, other types have their niche applications:
- Suspension Basket Evaporator: Ideal for solutions prone to crystallization or fouling due to its easier cleaning and maintenance.
- Multi-Effect Evaporators: Highly efficient in energy usage by reusing the vapor generated in one stage to heat the solution in the next.
- Direct Contact Evaporators: Suitable for specific processes where direct heat transfer is beneficial, like in certain chemical reactions.
Conclusion
The central circulation tube evaporator stands as the most widely used evaporator due to its combination of simplicity, reliability, and efficiency. Its versatility across various industries underscores its dominant position in the evaporation technology landscape. While other types serve specific needs excellently, the central circulation tube evaporator remains the go-to choice for many industrial processes, ensuring the seamless transformation of liquids into vapors.